With tools and technologies evolving at an unprecedented pace, a company’s success is often determined by their ability to keep up with the speed of innovation. Each advancement brings new efficiencies, new capabilities, and a need to learn and adapt.
This presents unique challenges to the modern working world, specifically in finding qualified talent. The organizations that best meet these challenges and stay at the forefront of innovation are the same companies disrupting their industries.
One thing these organizations are addressing better than their competitors is the skills gap. While companies are well-aware of the difficulties in finding engineering professionals with the right mix of education and experience, many are still left wondering how we got here it and how to close the gap.
Automation’s contribution to the skills gap
While there are many contributing factors to the growth of the skills gap (ranging from industry veterans retiring to a lack of interest from college-bound students), automation has been the primary reason for its recent surge. Of the 5.6 million manufacturing jobs lost in the US between 2000 and 2010, about 85% were due to automation, robotics, and technological advancement.
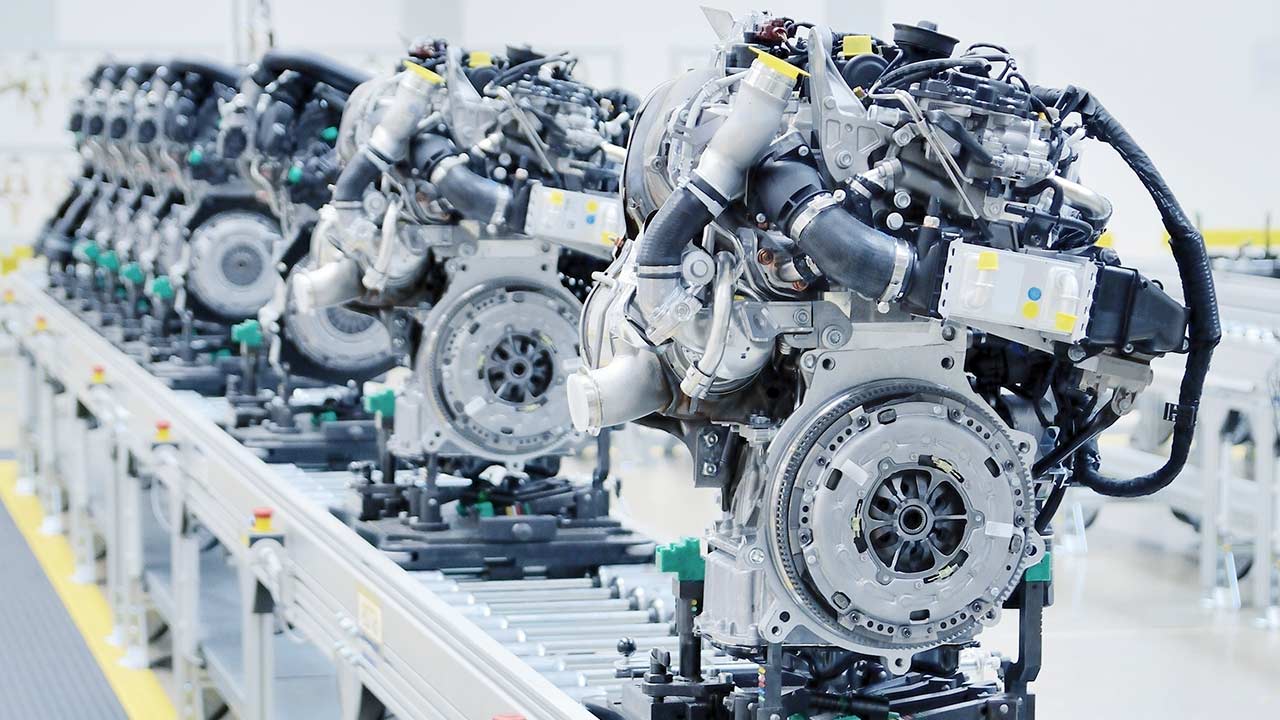
As these advancements become more prevalent and we rely more heavily on the use of technology in engineering and manufacturing, the demand for employees with more advanced training grows.
Despite these challenges in the workforce, investments in automation and software will only continue to increase. Over the last 20 years, the contribution of technological advancements in the US has helped to double the output of manufacturing workers.
Mireya Solís, a senior fellow at Brookings Institute, weighed in on this topic. “Simply put, we are producing more with fewer people. Automation has transformed the American factory, rendering millions of low-skilled jobs redundant. Fast-spreading technologies like robotics and 3D printing will exacerbate this trend.”
As the industry struggles to find a balance between the dwindling workforce and the benefits of automation, we face this question: how can both companies and individuals prosper in this rapidly advancing world?
Closing the gap with ongoing learning
To thrive in this new economy, organizations and individuals must embrace ongoing learning and training to stay competitive. By putting a targeted focus on ongoing learning, you can quickly adapt to changes in technology and create innovative products that can increase your market share.
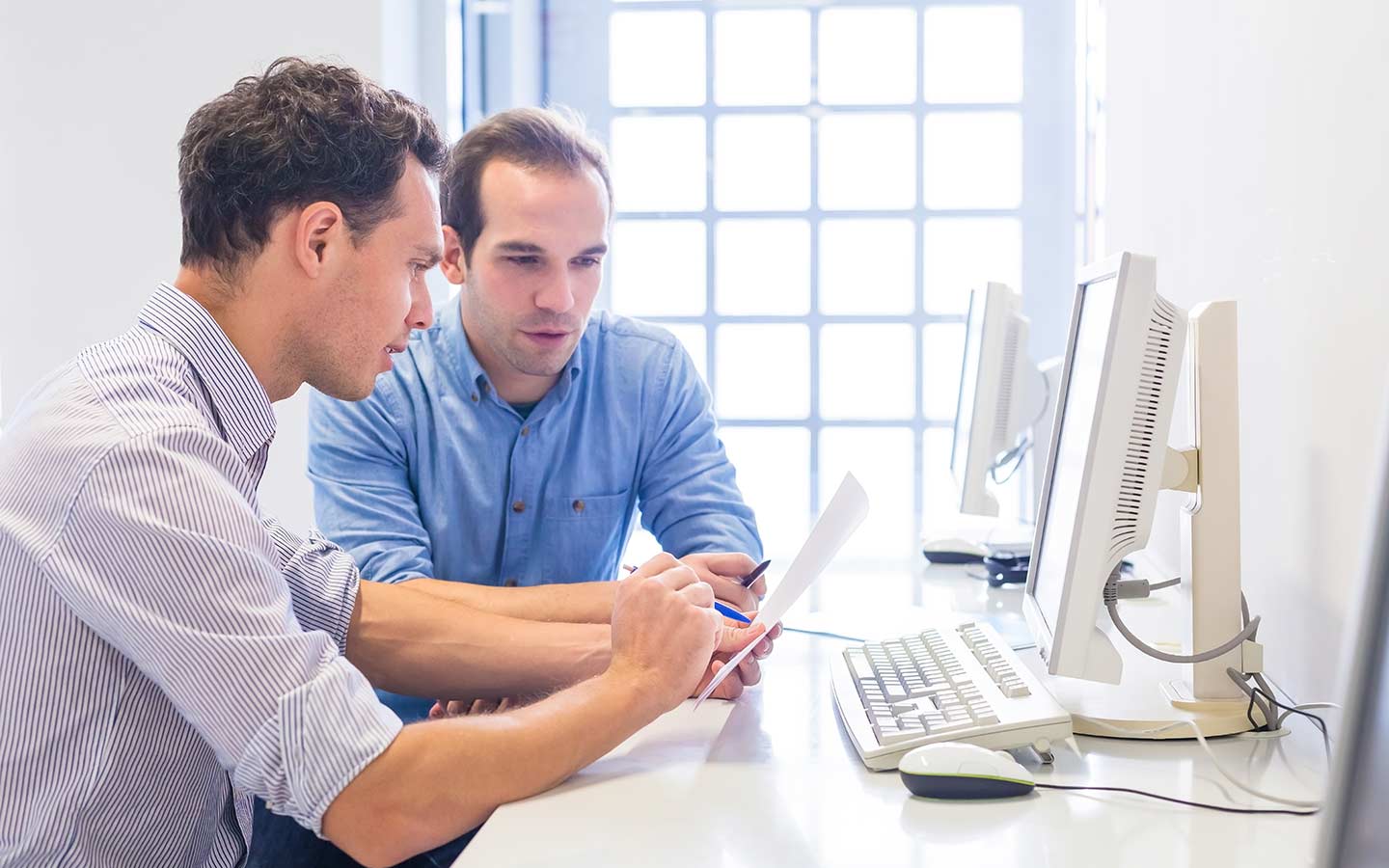
Ongoing learning ranges from mastering new software packages and techniques to establishing best practices within your organization. Standardizing training and design methods can significantly increase the efficiency of your team and their designs.
David Born, Director of R&D at Dow Chemical, heads up a team that has consistently won R&D awards year after year. He noted in a recent conversation that properly trained teams are free to think creatively and innovate, as they aren’t preoccupied with searching for answers to software-related problems and other day-to-day challenges.
In the end, a commitment to lifelong learning and ongoing training will help you and your company overcome the skills gap. Find people who are constantly looking to learn and improve, and provide them with the proper training and skills development tools they need to become masters in their field. David Blake of Degreed summarizes this brilliantly:
“The future depends on our commitment to be our best selves and discover our own personal missions. To become experts — each of us. The challenges of the future won’t care how you became an expert, just that you did. And that you made a difference.”