The crowd was anxious. I was in the back of the general session, but I could sense the excitement radiating from the audience. It was day one of SOLIDWORKS World 2018. Attendees were eager to depart for their breakout sessions and browse the Partner Pavilion, but before they could depart, Neri Oxman was scheduled to take the stage.
Oxman is a designer and architect, but she’s really so much more than those labels. The titles “sustainable world-builder” or “environmental redesigner” are much more fitting. She is at the forefront of
bio-informed design, material ecology, 3D printing, and art. Oxman and her research team, the Mediated Matter group, sit at the intersection of computational design, materials engineering, synthetic biology, and additive manufacturing. Oxman applies knowledge from these disciplines to explore design, while teaching at the MIT Media Lab has given her access to the funds needed to turn her ideas into tangible designs.
When Oxman appeared on stage, she launched into an enthralling and inspiring lecture on her design inventions. She rattled off creations – 3D printed wearable capillaries designed to provide interplanetary travelers with organisms needed to sustain life, biodegradable objects made up of chitosan (shells of crustaceans combined with an alkaline substance), and a silk pavilion that was made using algorithms to direct silkworms. Everything she does is artistically beautiful with the potential for practical applications, but the highlight of her talk revolved around glass.
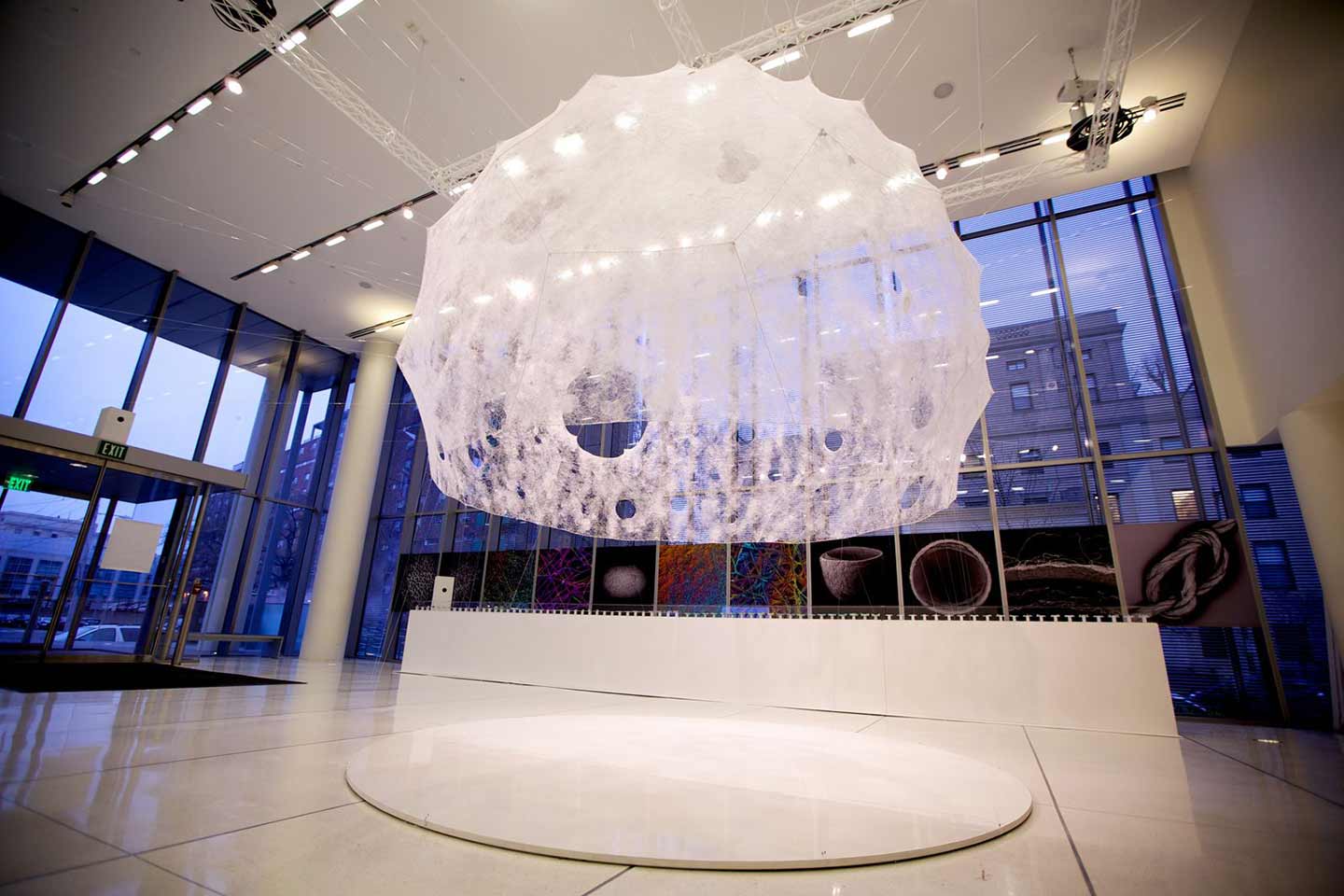
Oxman and Mediated Matter set out to create a printer and printing process that could successfully develop optically transparent glass components. Revolution in manufacturing has historically occurred when the constraints of fabrication have been broken. Additive manufacturing has broken a lot of constraints, but the melting point of glass and the delivery limitations of filaments have proved to be significant hurdles to overcome. The Mediated Matter team set out to break the limitations of glass manufacturing and additive manufacturing. In 2015, they revealed the culmination of their work, the G3DP. A 3D printer that can print optically transparent glass.
GLASS I. The Mediated Matter Group. 2015
The G3DP
The printer is unique in its usage of a gravity-driven kiln cartridge, which consists of the crucible kiln and the nozzle kiln. Molten glass is added to the crucible kiln through a removable lid and gravity directs the glass through the heated kiln. A ceramic nozzle is attached to the bottom of the crucible kiln similar to a typical FDM 3D printer. The nozzle kiln controls the flow of glass, guaranteeing glass adhesion and filament diameter; therefore, reducing printing defects. The crucible and nozzle kilns are maintained at around 1900°F and as the molten glass flows on to the ceramic print plate, it cools and hardens. Lowering the nozzle temperature stops the flow of molten glass.
Rendered cross section showing (A) the printer during fabrication, (B) the kiln cartridge, (C) the crucible kiln, and (D) the nozzle kiln. Detail elements are as follows: (1) the crucible, (2) heating elements, (3) the nozzle, (4) the thermocouple, (5) removable feed access lid, (6) stepper motors, (7) printer frame, (8) print annealer, (9) ceramic print plate, (10) z-drive train, (11) ceramic viewing window, and (12) insulating skirt.80/20 aluminum stock and a square steel tube make up the frame of the printer, and the XYZ motion is dependent on stepper motors that are controlled electronically by an Arduino and a RAMPS 1.4 Arduino shield. The nozzle operates on the X and Y-axis, and the ceramic plate descends to provide Z-axis (vertical) movement. Mediated Matter upped the ante with the release of the G3DP2 in 2017 which is four times larger than the original G3DP. The newest printer includes a digitally integrated thermal control system which facilitates various stages of glass forming. Faster production rates, enhanced precision, and flow control, combined with the ability to print 30kg(!!!) of molten glass in one sitting, means one badass and innovative printer.
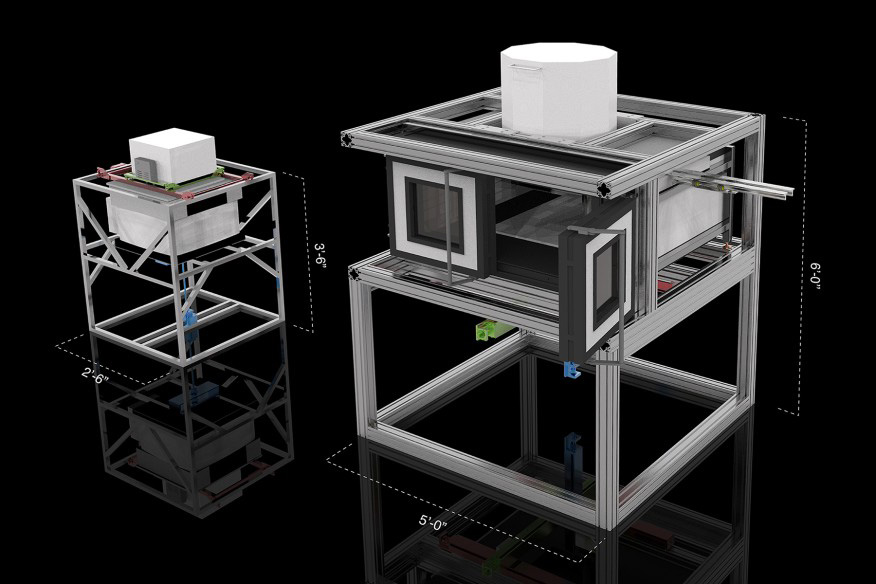
The parametric software environment attached to the printer tells the team the time and temperature gradients needed to produce specific shapes. Their 3D objects are normally created in
Rhinoceros 5.0 and sliced into a helix using a custom C# script to accommodate the continuous flow of a specific diameter of glass. Glass viscosity data determines operating temperature, and Solidworks Flow Simulation was used to obtain the necessary temperature distribution needed to successfully print the object.
Oxman and her team began to explore the capabilities and limitations of glass printing once the specs of her printer were established. They discovered that flow rate could be reduced to increase layer width, the optimal molten glass feed rate differed from the flow rate, and parts with draft angles up to 40° could be printed under optimal conditions. Later, they identified that the distance between the print plate and the nozzle could be increased to create waves, loops, and ropes of glass. The speed of the glass flow relative to the speed of the nozzle’s movement could be adjusted to create different paths of loops, coils, and waves. Color could be integrated into the glass through paint frits, granulated ceramic compositions used to deliver pigment, added in sequence to give objects a color gradient without disrupting the printing process. This was the beginning of their quest to demonstrate the capabilities of glass 3D printing.
Glass II
The culmination of their work was showcased in 2017 at the Salone del Mobile, in Milan, Italy. Vertical glass installations were produced at an architectural scale, approximately 10 feet tall, for the Lexus Yet exhibition. These “columns” were made up of multiple stacked glass petal objects that were around eight inches tall. The profile of the column changes as you move up the column. A six-petal base turns into three petals as your eyes move to the pinnacle of the column, an eight-petal base turns into four petals, and so on.
The different column forms are demonstrating the ability to print glass that is determined by desired mechanical and optical properties. The exhibit explains that “the higher the load, the greater the surface area of a column in plan view, the greater the number of lobes desired, the tighter the turning radius required for their 3D printing, and hence contributing to the geometric expression of the caustics.” In a video that documents and details the installation, one of the eight petal components doesn’t begin to crack until the load placed upon it reaches 250,000 pounds.
GLASS II. The Mediated Matter Group. Milan Design Week, 2017Inside each column is a lighting system that travels up and down creating a psychedelic, kaleidoscopic projection on the exhibit walls and floor as the light rays reflect and/or refract through the 3D printed glass. The projection is constantly changing because of the glass curvature, the vertical petal variation, and the way viewers inhabit and interact with the space.
If we can print optically transparent glass at architectural scale, we can potentially harvest solar energy. Creating inner channels and inner pockets within the architectural scale glass models could be used in conjunction with color to absorb light and heat. Oxman sees the ability to independently control the inner and outer surface textures as a method for controlling solar energy. Imagine the exterior of a glass building being optimized to harness solar power by
leasing solar panels which often tend to zero out the costs of renting them in any sunny area.
The work of Neri Oxman and Mediated Matter appear in art installations and exhibitions around the world. The next step is to take what has been developed and practically apply it on a significant architectural scale. I believe her willingness to take risks and her multidisciplinary background will translate to commercial success if she decides to go that route. But for now, I am happy to sit here and be mesmerized by her atypical installations and hypnotized by the coiling flow of molten glass.
Share this post