This article was written by the team at Xometry, a custom manufacturer and on-demand service provider for 3D printing, CNC machining, and more.
Over the past decade, 3D printing has become more prevalent in all manufacturing industries. This is due to the many unique advantages that 3D printing has over subtractive manufacturing processes like CNC machining. One of the key benefits of 3D printing is its ability to replace complex traditional assemblies with individual parts. In the past, creating components with complicated internal geometries required complex sub-assemblies of many interconnecting parts. This article will describe how to reduce 3D printing costs by reducing the overall part count, and will shine a light on the benefits of lower part counts in products.
3D Printing Technologies
3D printing is a term that covers a wide range of additive manufacturing technologies. As such, it is important to understand the main differences between the various technologies since each is intended for specific applications. However, all of the technologies listed can lower 3D printing component count.
- Laser Sintering (LS) – This is a subclass of Powder Bed Fusion printers that use a high-energy laser to slowly build up a part by fusing powder layer by layer. This powder can be plastic (Selective Laser Sintering, SLS) or metal (Direct Metal Laser Sintering, DMLS). This technology allows for complex internal geometries because excess powder can simply be poured out of any internal areas after printing.
- Fused Deposition Molding (FDM) – This method of 3D printing is the most recognizable since many desktop 3D printers use it. As a material extrusion process, a filament of plastic is fed from a spool through a heated nozzle to build up a part layer by layer. Parts made using FDM 3D printing are more limited when it comes to internal geometries and complex shapes because overhangs need to be supported by printed support structures.
- Stereolithography (SLA) – This makes use of a vat of UV-sensitive liquid polymer that is solidified by exposing it to a laser or UV light. SLA is part of a family of processes using Vat Photopolymerization to create parts layer by layer. SLA is capable of producing small complex features and generates a smoother surface finish than other 3D-printer technologies.
- Polymer Jetting (PolyJet) – Polyjet printing can print in multiple materials and colors at once. A form of material jetting, this process works by specifically depositing small droplets of a liquid polymer onto the build platform in a manner similar to inkjet printing. This polymer is then instantly cured with a UV light. Material properties and colors can be adjusted by depositing different blends of materials in micro-matrices.
- Multi Jet Fusion (MJF) – This technology from Hewlett Packard (HP MJF) works via Powder Bed Fusion but does not use a laser to melt the individual powder particles together into a final part. Instead, the powder is maintained at a temperature close to its melting point, and a fusion and detailing agent is jetted onto the powder. Immediately after that, a heat source is projected onto the plastic and only the areas with the deposited agents melt, thus allowing that bit of powder to solidify into the desired shape.
- Digital Light Synthesis (DLS) – A process from the company Carbon, DLS is a unique printing technique based on Vat Photopolymerization that makes use of continuous production from a liquid resin to produce parts. Formerly called Continuous Liquid Interface Production (CLIP), this process can print isotropic engineering thermoset materials. After the print is complete, the part is further cured in an oven to achieve its ultimate mechanical properties.
How 3D Printing Reduces Part Cost
- Reduced Material Waste – Unlike subtractive manufacturing that starts with a billet of material and machines away excess material, additive manufacturing or 3D printing slowly builds up a part with little or no waste material. This results in reduced material cost per part. The savings compound when a multi-part assembly can instead be consolidated and printed as a single component.
- Reduced Labor Costs – With any subtractive manufacturing process there are significant costs related to labor. Skilled operators are required to mount the raw material into the machine and monitor it during machining. This labor cost is multiplied by the number of components required for an assembly of parts. A single 3D-printed part requires far less labor input than an assembly of CNC-machined parts, thus reducing labor costs.
- Reduced Fabrication and Assembly Time – Modern CNC machines are extremely fast, but their setup takes time. 3D printing requires minimal setup, so parts can be produced much quicker. Additionally, if a product is made up of multiple individual parts, care must be taken to ensure that all these parts meet the relevant tolerance ranges to ensure proper fitting. This adds additional inspection time. The replacement of assemblies with single-piece printed elements reduces this inspection time-drain.
How to Lower 3D Printing Component Count
Newer manufacturing technologies are driving engineers to explore design options that were not possible with traditional manufacturing technologies. Design tools like generative design and topological optimization allow engineers to explore the theoretical limits of engineering by simply specifying a range of governing parameters. Algorithms then iterate through thousands of increasingly optimized designs to present engineers with a range of options that meet the input parameters. These designs are often single-part structures and very organic in nature, allowing them to significantly lower 3D printing component count.
Apart from algorithmic solutions, engineers can create single-part designs from scratch. Complex internal geometries can be designed into products with less concern about access for assembly.
Benefits of Lowering Part Count
Listed below are five benefits of lower 3D printing component counts in addition to lower costs:
- Parts are more mechanically robust and less prone to coming loose and failing.
- Complex assemblies can introduce a range of foreign object debris within the machine that can cause damage and reduce performance.
- Lower 3D printing component counts make lightweighting efforts much easier – a critical consideration in weight-sensitive industries like aerospace, robotics, or wearables.
- Low part numbers make for simpler spare-parts management and reduced inventory requirements. Maintaining a large, slow-moving inventory is economically risky.
- Tolerance stack-up can add significant complexity to manufacturing. With reduced part counts there are fewer tolerance-accumulation challenges.
Case Study in Reducing Part Count: Boston Dynamics
The robotics industry is rapidly growing as more and more companies look to automation to stay competitive. One of the most visible companies in the robotics sphere is Boston Dynamics, who develop a range of highly capable robotics systems. Their bipedal robot dubbed “Atlas” contains a large number of 3D-printed metal components. As indicated in the images below, the feet and torso of the robot are manufactured as single parts. Typically, each of these would have been complex assemblies of individual parts and fasteners. In addition to using fewer components, the leg can be manufactured to include internal chambers for fluids and electronics.
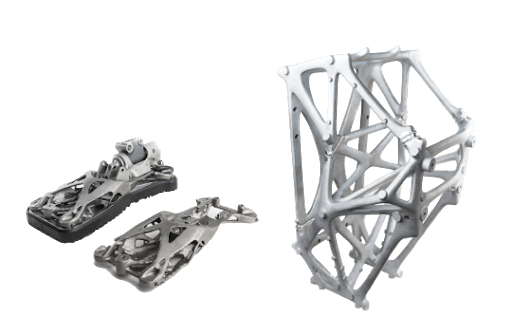
Robotic part design of Atlas, the humanoid robot from Boston Dynamics, using metal 3D-printed parts.
(Image Source: Boston Dynamics)
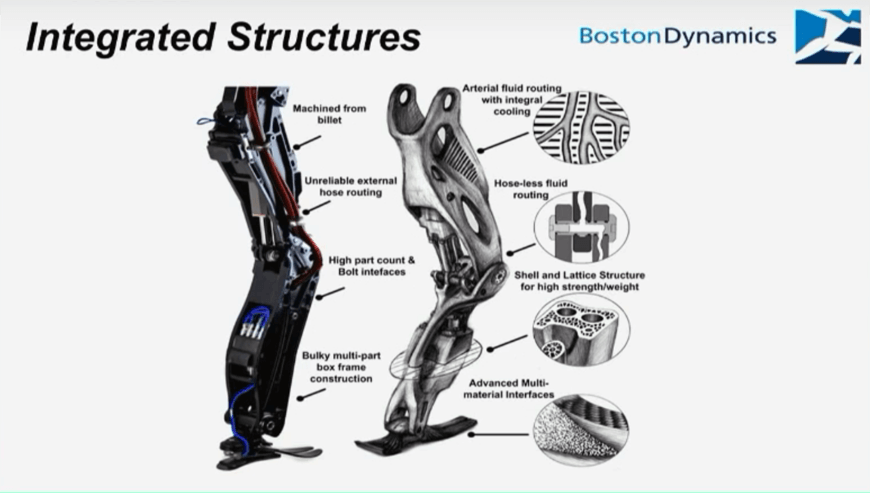
Comparison diagram of a robotic leg with assembled metal components versus a metal 3D-printed robotic leg.
(Image Source: 3D Printing Industry)
Key Considerations
It must be noted that 3D printing is not yet at the point where it can replace subtractive technologies completely. This is largely due to the following factors:
- Precision: 3D-printed parts are typically not as precise as parts created on advanced CNC machines. 3D-printed metal parts often require secondary operations on CNC machines to achieve tight tolerances.
- Strength: Most printed metal parts compare favorably with CNC-made parts in terms of strength. However, plastic prints in general do not match up when compared to injection-molded or machined plastics due to anisotropic properties inherent in many 3D printing processes.
3D printing is ideal for creating anything from visual prototypes to fully-functional parts. To learn more about how 3D printing can be a force multiplier for your product development or manufacturing requirements, or to learn how to reduce 3D printing costs and submit a quote request, contact a Xometry representative.