This article was written by the team at Xometry, a custom manufacturer and on-demand service provider for 3D printing, CNC machining, and more.
There are many ways to make a metal part. Among the most cost-effective and versatile techniques is the use of sheet metal. As with many other manufacturing techniques, parts often need to be post-processed or finished after they have been fabricated to enhance their physical or aesthetic properties. This article will discuss the different manufacturing finishes for sheet metal as well as their benefits and applications.
Steel is one of the most widely used materials in manufacturing due to its strength, durability, and versatility. Whether for industrial applications, construction, or custom metalwork, steel components often require finishing techniques to enhance their performance and longevity. Processes such as galvanizing, powder coating, and anodizing help protect steel from corrosion, improve its appearance, and ensure it meets the specific requirements of its intended use. The right finish not only extends the lifespan of steel products but also adds to their functionality by making them more resistant to wear and environmental conditions.
Businesses requiring precision metalwork, stainless fabrication services offer expertise in creating high-quality steel components tailored to various industries. From custom sheet metal projects to large-scale industrial fabrication, these services ensure that steel parts are designed and finished to meet the highest standards. Whether for architectural structures, machinery, or specialized equipment, working with professionals in stainless fabrication services guarantees a level of craftsmanship and durability essential for long-term performance.
Manufacturing finishes for sheet metal
When deciding on the best finishes for sheet metal parts, it’s important to understand your options. Listed below are some of the more common finishing processes specifically used on sheet metal parts. Many of these surface finishes offer improved corrosion resistance. Corrosion resistance is a general term, however, and an object’s overall resilience will depend on many factors. These may include the environment, the corrosive medium, its concentration, and the level of exposure. To determine which finish is best suited to your specific application, click here.
GET STARTED: Learn Sheet Metal Design for Autodesk Inventor with this Online Course >>
1. Standard Finish
As the name indicates, a standard finish means that nothing is done to the final part in terms of finishing. This manufacturing finish for sheet metal is usually done when the base material is already suitable for the application environment. A good example is a stainless steel 316 part. Even used in a corrosive environment, it generally would not need additional finishing (apart from pickling and passivation) because the metal itself is well-suited to corrosive environments. Another reason not to finish a part is that the material’s natural appearance is considered desirable.
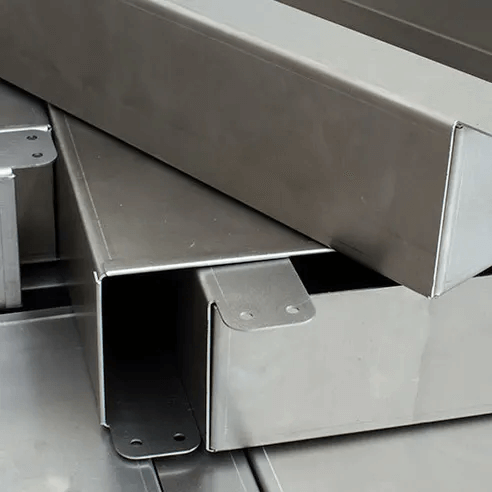
Figure 1 – Standard Finish (Image Source)
2. Bead Blasting
Bead blasting is less aggressive than normal sand/grit blasting and uses sand or glass beads as the abrasive medium. The air pressure is also lower than other blasting processes and thus it removes less material from the surface of the part. The purpose of bead blasting is to clean off any tool marks or other unsightly blemishes and achieve a uniform surface finish. Bead blast also can mask grain direction on sheet metal, which is useful for creating a consistent look for laser cut metal parts. Bead blasting is often considered one of the more aesthetically pleasing manufacturing finishes for sheet metal and results in a matte finish.
FREE E-GUIDE DOWNLOAD: 8 Steps to Transform Your 3D Models into Sheet Metal Designs >>
3. Anodizing
Anodizing is the process of converting the surface layer of the metal into an oxide. These oxide layers are very thin when compared to other coating methods, but are still extremely durable. The most commonly anodized material is aluminum. Anodizing can be classified into three main types and each type is further broken into two classes.
- Type 1: This anodizing process is not as common as the other two types. It essentially creates a thin, highly corrosion-resistant coating typically for aerospace applications.
- Type 2 (Class 1 & 2): This process results in a thin oxide layer that can easily be dyed with different colors for cosmetic purposes. It also gives the anodized part corrosion resistance. Class 1 refers to un-dyed and Class 2 refers to dyed coatings. Although black is the most popular Type 2 anodization, there are clear, blue, red, gold, yellow, orange, green, purple, and other pigments available.
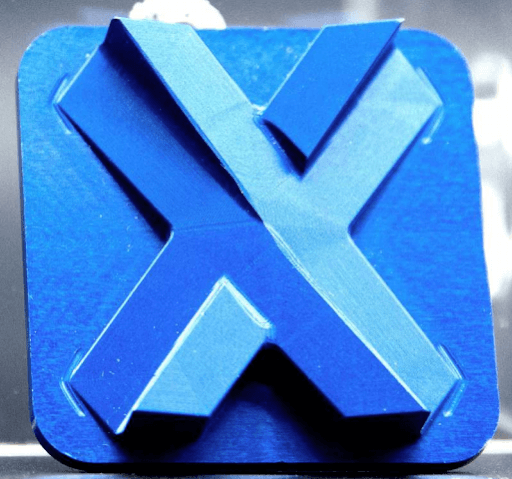
Figure 1 Type 2, Class 2 Blue Anodized (Image Source)
- Type 3 (Class 1 & 2): Type 3 anodizing results in a much thicker coating (approximately two to four times thicker than Type 2). As a result, this type of coating is more wear-resistant than Type 2 while also retaining the same corrosion resistance. Class 1 refers to a clear hard coat whereas Class 2 refers to a black hard coat.
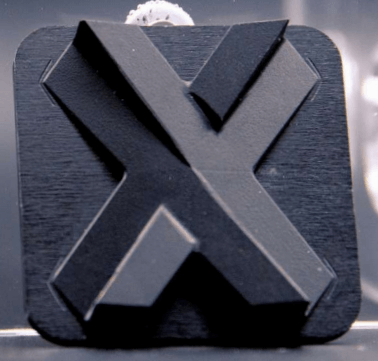
Figure 2 Type 3, Class 2 Black Hardcoat (Image Source)
Anodizing is one of the most versatile manufacturing finishes for sheet metal parts as it offers both wear and corrosion resistance. Xometry offers both Type 2 and 3 coatings.
4. Chemical Film Coating
Chemical film coatings are described as sealant coatings and therefore can only offer corrosion resistance. They do not confer any additional wear resistance. The chemical films have the added benefits of maintaining electrical conductivity and enhancing the bonding of paint and powder coatings to the base material. Anodized finishes can be applied over chemical film coatings. Here are the chemical film classifications:
- Type 1: This type of coating is used infrequently since it contains hexavalent chromium (a tightly controlled chemical) and results in a gold or brown coating.
- Type 2: Type 2 chemical film coating uses titanium, zirconium or trivalent chromium and results in a clear coat. This is typically the standard chem film coating used in aerospace and military applications.
- Class 1A: The primary purpose of this coating is to improve the corrosion resistance of the base material while simultaneously being used as a primer for decorative or corrosion-resistant paints. This coating is typically thicker than Class 3 coatings.
- Class 3: Class 3 coatings are designed to provide increased corrosion resistance without compromising electrical conductivity.
The MIL-DTL-5541 chemical film coating standard does not include a Class 2 classification.
5. Powder Coating
While not as good as anodization or chemical films when it comes to corrosion resistance, powder coating offers a wide range of colors for aesthetic purposes and is generally more corrosion-resistant than paint. This is, in part, due to the fact that the powder is baked into the top layer of the material, creating a stronger bond than can be achieved using paint. Powder coating has one of the widest color ranges when compared to other manufacturing finishes for sheet metal.
SEE WHAT’S NEW: Explore New & Improved Sheet Metal Features with SOLIDWORKS 2021 Update Training >>
6. Electroless Nickel Plating
As the name suggests, this type of coating does not use the electrolytic effect to plate materials. Instead, a chemical bath is used to plate the part.
The nickel coating has varying degrees of phosphorus content that can improve the corrosion resistance while sacrificing hardness and, by extension, wear resistance. The chief benefit of this coating type is that it uniformly covers all surfaces, including those that cannot be effectively or reliably reached with some of the other coating methods listed. As such, it is one of the better-suited manufacturing finishes for sheet metal parts with complex shapes. Electroless nickel plating can also be used on a wider array of metallic surfaces. This finish can be further subjected to heat treatment to improve its mechanical properties.
7. Gold & Silver Plating
Gold and silver coatings are applied to a metal part using an electroplating process.
Gold is an excellent conductor with the added benefit of corrosion, tarnish, and oxidation resistance. This makes it an ideal coating for electrical contacts. In addition, gold has excellent solderability, further improving its utility in electronic components. Gold plating is divided into different types and classes. The types generally refer to the purity of the gold used in the plating and the classes refer to thicknesses.
Silver plating offers some advantages over gold plating. It has better electrical conductivity and is cheaper than gold plating. However, this manufacturing finish for sheet metal is susceptible to oxidation that will ultimately reduce its electrical conductivity.
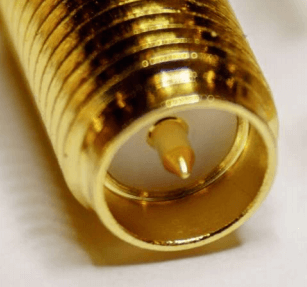
Figure 3 – Gold Plating (Image Source)
Xometry offers access to a wide range of manufacturing finishes for sheet metal parts through their extensive Supplier Network. Xometry has streamlined the process of obtaining quotes from approved Suppliers. This allows you instant access to prices, lead times, and a huge selection of manufacturing options. If you are unsure of which finish or manufacturing specifications are best for your application, contact a manufacturing expert at Xometry who can leverage wide industry knowledge to help you find the ideal finishes for your sheet metal parts.