Industry 4.0 technologies are transforming the world of manufacturing. To celebrate Manufacturing Day, here are three of our favorite innovations so far.
Industry 4.0 is upon us, bringing with it waves of new digital industrial technology that are already transforming manufacturing around the world. If you need a quick refresher, here’s a list of the biggest Industry 4.0 technologies that will be at the helm of these transformations:
- Big data and predictive analytics
- Robotics
- Artificial Intelligence (AI)
- Augmented and virtual reality
- Industrial Internet of Things (IIoT)
- Horizontal and vertical system integration
- Additive manufacturing
- Automation
Organizations in all sectors of manufacturing are adopting technologies like these to make their production processes and facilities more intelligent, fast, flexible, and efficient. In this article, we’ll explore some of our favorite uses of these innovative technologies from cutting-edge manufacturers that are already making an impact.
>> Discover the Truth Behind Some of the Biggest Myths about Manufacturing Jobs
Smart Factory: Whirlpool + Schneider Electric
Smart factories are exciting innovations because they encompass many (if not all) of the Industry 4.0 technologies. Smart factories use automation, robotics, and additive manufacturing to manufacture products more quickly and efficiently, but they also use the IIoT and predictive analytics to optimize processes and make better data-driven decisions.
This is what makes the Whirlpool smart factory so innovative. Whirlpool, a manufacturer of home appliances, teamed up with Schneider Electric to implement their resource monitoring software, EcoStruxure™ Resource Advisor, in their manufacturing plants. This software collects and analyzes data from all kinds of equipment. This data not only helps Whirlpool get a better view of their ROI on resources, but it also helps them to achieve ambitious sustainability goals. The advanced analytics identify areas where resources, primarily water, are being wasted and also help them find solutions to be more efficient. Whirlpool is anticipating over $1 million in savings in three years just by identifying recyclable waste in its Ohio factories.
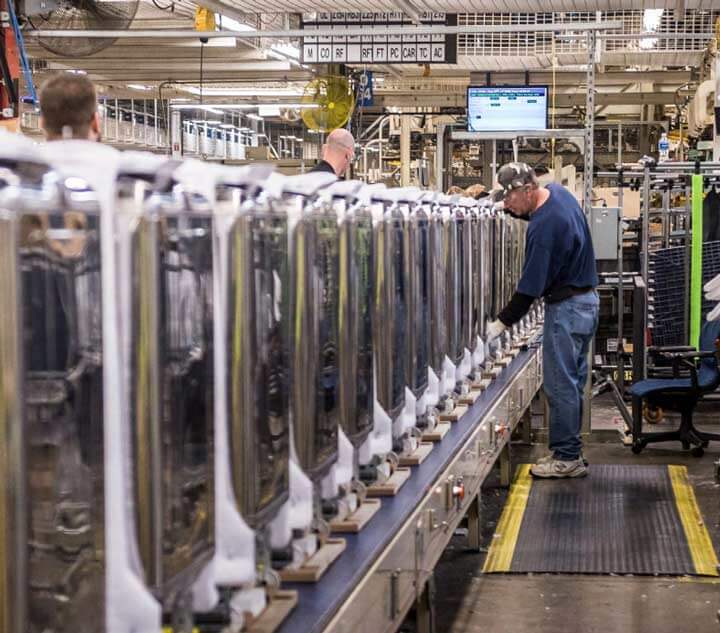
Whirlpool smart factory. Image: AltEnergyMag.com
Additive Manufacturing: Fast Radius + Husqvarna Group
The applications for additive manufacturing are vast and the impacts are huge, with the market growing quickly and projected to reach over $23 billion globally by 2026. Methods like rapid prototyping significantly reduce production time and costs. New applications are being discovered all the time that are faster and more efficient than traditional methods.
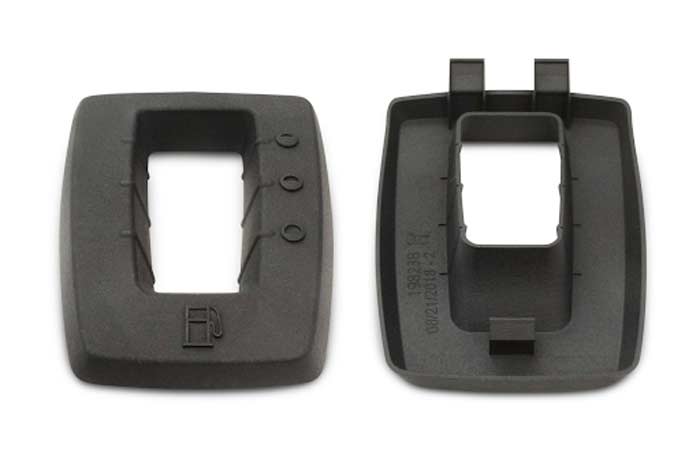
Spare parts produced through additive manufacturing. Image: Fast Radius
One such application is the Fast Radius Virtual Warehouse. Fast Radius has worked with Husqvarna Group, a power tools producer, to transition their spare parts production to an additive manufacturing solution. This “virtual warehouse” means spare parts can be manufactured on-demand so they are never out of stock. This essentially eliminates inventory costs (a major pain point for many manufacturers) and helps reduce material waste.
>> Don’t forget these 3 Additive Manufacturing Design Factors You Need to Consider
Artificial Intelligence: Airbus + Autodesk
AI often brings high-tech images to mind, but AI in an industrial setting is probably not the application people think of first. However, there are many innovative applications for AI in the manufacturing world. One of the most promising is generative design. Generative design is a form of AI that allows engineering designers to input design goals and parameters into 3D modeling software and then quickly receive design alternatives.
Airbus and Autodesk have developed a 3D-printed airplane cabin partition using generative design technology. While it might sound like an insignificant part of a plane, the partition is actually a tricky piece to manufacture. It must be lightweight while still strong enough to support jump seats for the crew during take-off and landing. Using generative design enabled Airbus to create a new, alternative design for the partition that met those requirements and then some. The new design is 45% lighter and requires 95% less raw materials to manufacture. Ultimately, this reduces fuel costs and improves the carbon footprint of the plane.
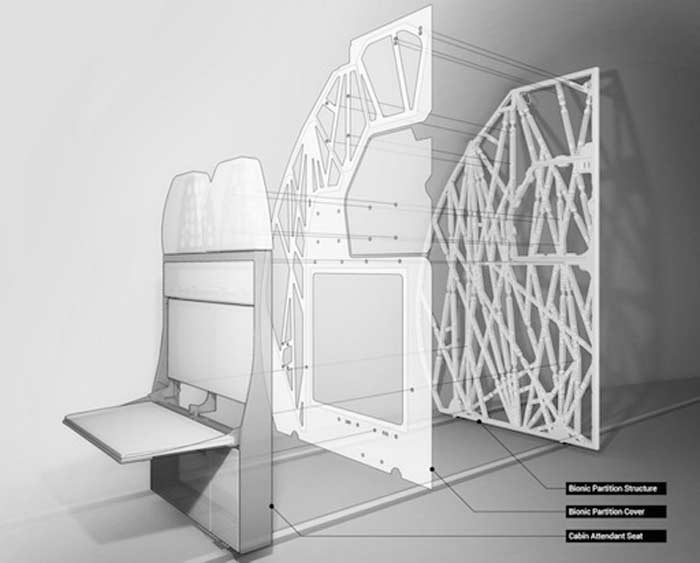
The Airbus 3D-printed partition. Image: Airbus
These are just the beginning! Countless other Industry 4.0 innovations are being developed every day. One thing’s for sure: it’s an exciting time to be in manufacturing!
This article is part of our #MFGDay19 series! We’re celebrating the manufacturing industry all month. Check out other articles from the series here:
- 3 Additive Manufacturing Design Factors You Need to Consider
- Why the Manufacturing Industry Needs to Close the Gender Gap in Order to Defeat the Skilled Labor Shortage
- How Employers Can Attract Fresh Engineering and Production Talent to the Manufacturing Industry
- The Truth Behind Some of the Biggest Myths about Manufacturing Jobs
- Everything You Need to Know about Apprenticeship Programs (and Why You Might Want to Start Applying Now)